Nov 13, 2024
In-line quality control of Roll-to-Roll manufactured multilayer stack
In-line layer thickness measurement of a tri-layer system on PET under vacuum
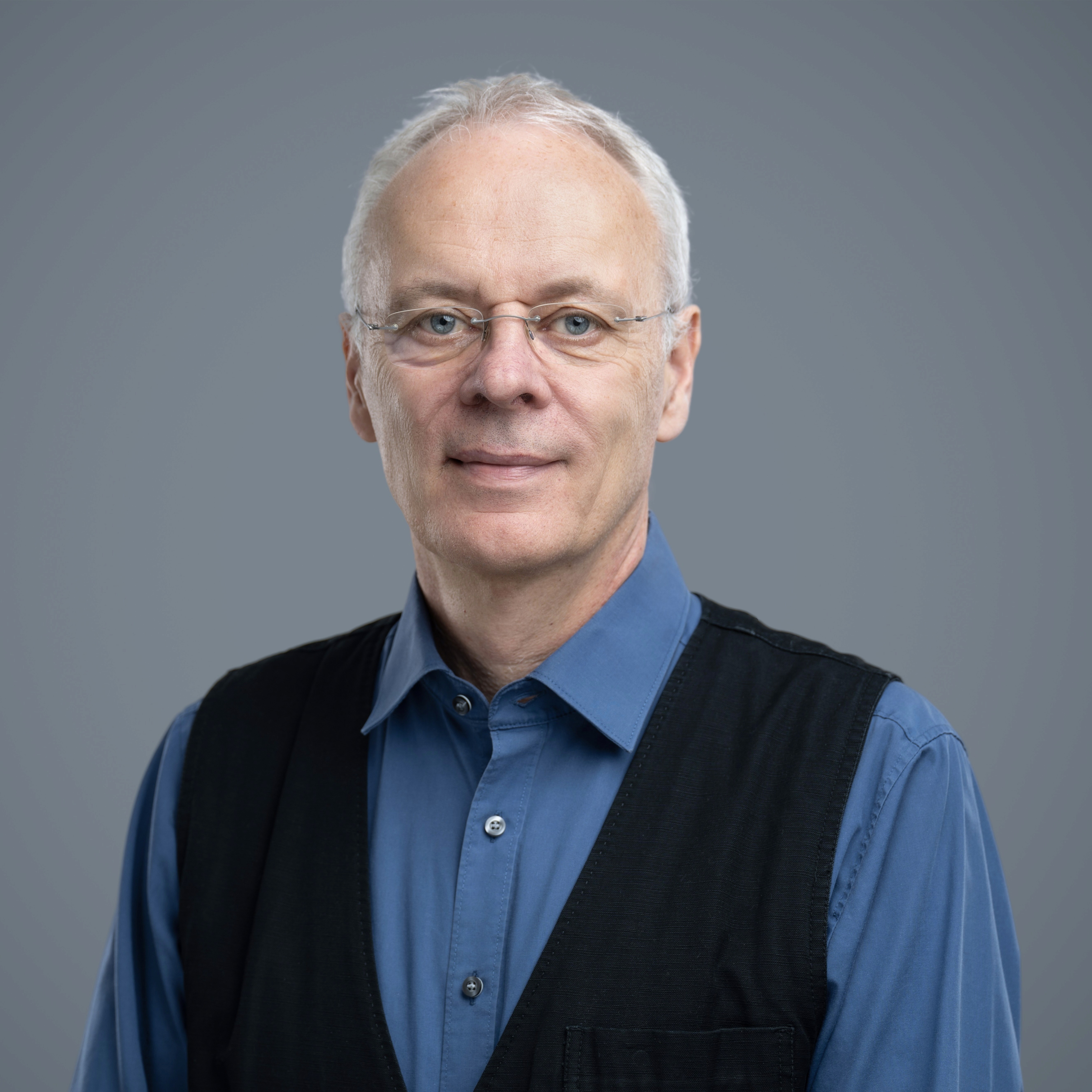
Dr. Wulf Grählert
Sales and Customer Care
Roll-to-roll (R2R) manufacturing is the prevalent process for high-throughput production of flexible substrates, including applications such as packaging foils, metallic foils, and flexible perovskite solar cells. High-precision deposition of layers with nanometre-scale thicknesses is typically achieved by vacuum R2R magnetron sputtering. This process involves the controlled ejection of target material via ion bombardment, facilitated by a magnetic field to enhance ionisation efficiency, resulting in precise deposition onto the flexible substrate within a vacuum environment.
High-precision applications with stringent quality requirements are often hindered by the absence of comprehensive in-line quality control with real-time data analysis. Current methods rely on costly and complex downstream metrologies, employing either single point in-line measurements or destructive off-line characterization techniques. This case study examines a multilayer stack of zinc tin oxide (ZTO), silver (Ag), and indium tin oxide (ITO) sequentially deposited onto a 125µm thick, 220 mm wide, unheated polyethylene terephthalate (PET) substrate with a length exceeding 100 m (see image below).
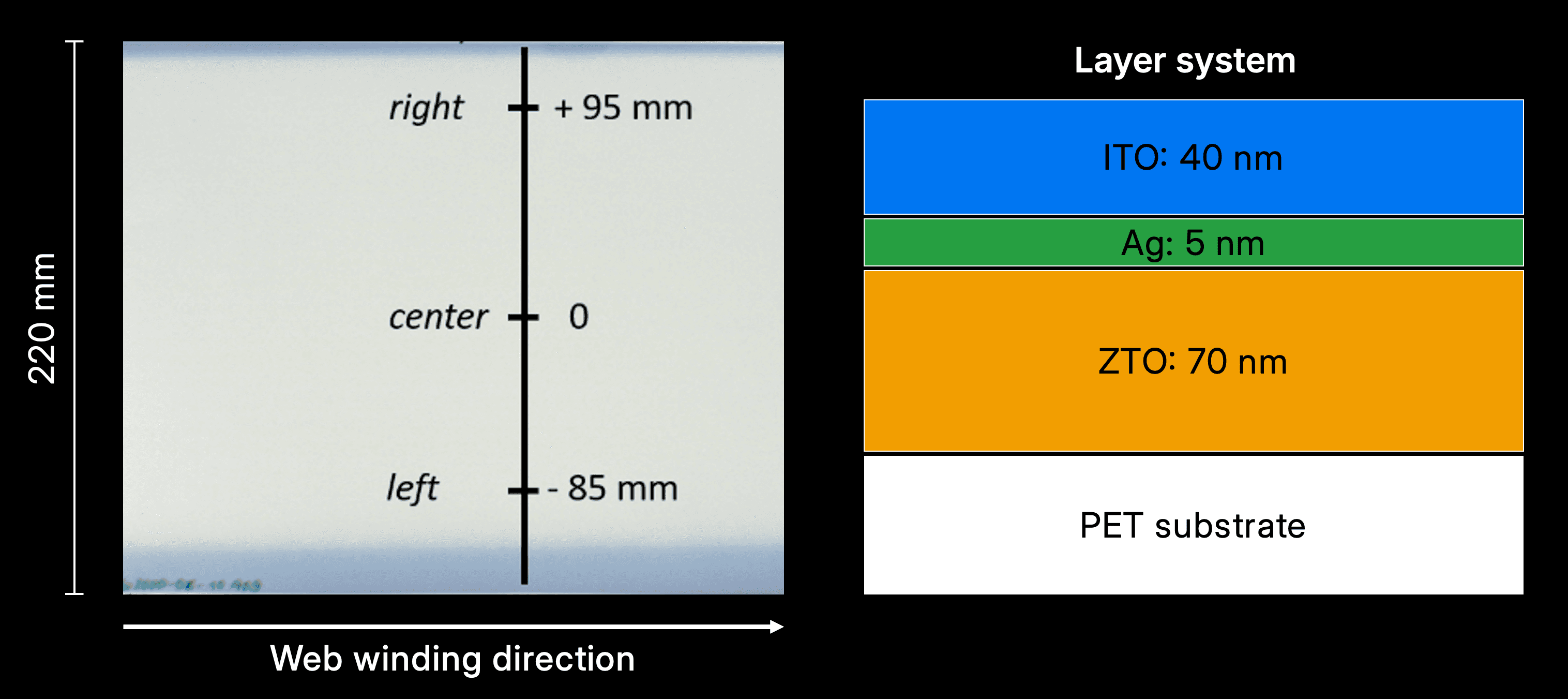
Currently, X-rax reflectometry (XRR) is used to inspect the thicknesses of each layer after production by extracting cut outs and laminating them onto a glass substrate. For each position on the belt three cut outs are extracted: in the centre and 100mm from the centre to each side. The measurement spot of XRR has a size of 1mm x 8mm. The following diagrams show the layer gradients of ZTO, Ag, and ITO sublayers, with variations attributed to measurements taken from five distinct samples.
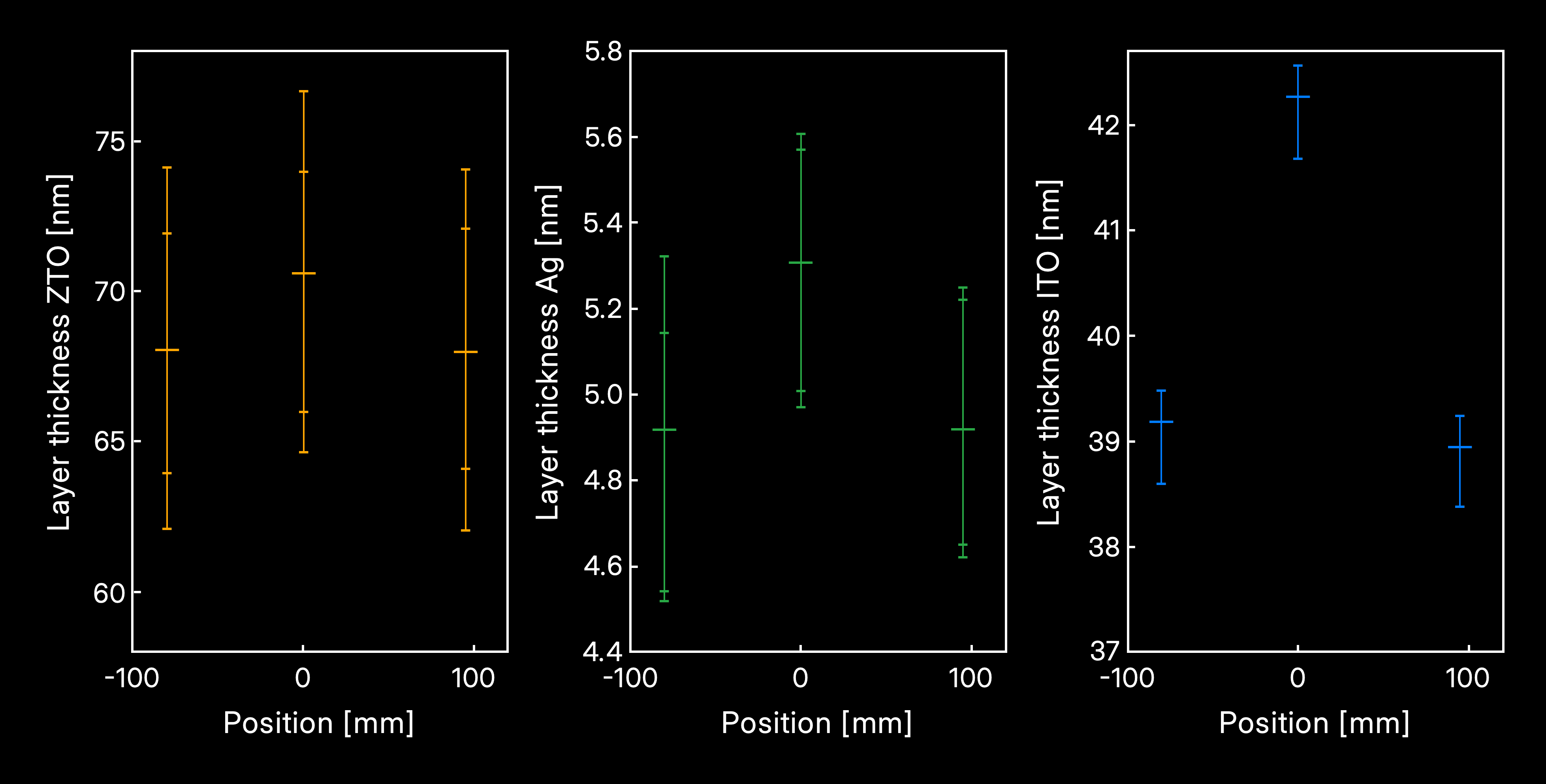
DIVE's solution
Our at-line VEpioneer and in-line VEreveal systems allow to determine the layer thickness of each sublayer with pixel-level precision in real-time. A sample of 220 mm width and 115 mm length is analysed non-invasively in less than 5 seconds, with a spatial resolution of 170 µm x 170 µm per pixel. This enables 100% in-line inspection.
The below image presents the analysed sample, where colour mapping visualises the layer thickness of ZTO, Ag and ITO per pixel. The visualisation highlights the ZTO base layer's homogeneity and the characteristic peak formation in both the Ag and ITO layers. This analysis achieves a root mean square error below 1 nm per individual layer. Increasing the sample size could further improve the observed R-square value of 0.85. The data also allows for extending the analysis to other characteristics beyond layer thickness such as density or roughness through inspecting crystallinity and phase composition.
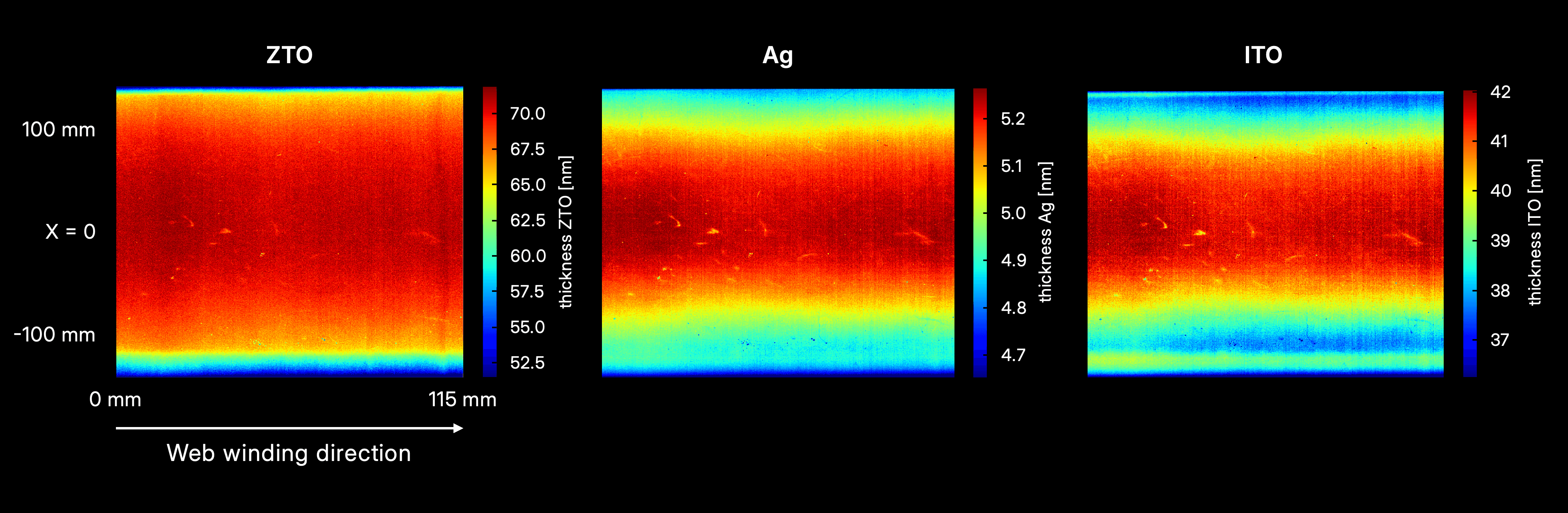
VEpioneer and VEreveal are built upon identical technological foundations and utilize our proprietary software suite, VEsolve Pro. The image below illustrates the operational workflow. Initially, data acquisition is performed via line-scan hyperspectral imaging, wherein the intensity of light reflected by the excited sample is measured. Spectral decomposition occurs within the camera, recording the intensity per pixel. Subsequent frame acquisition through sample translation results in the formation of the hyperspectral data cube. In the second phase, this data undergoes screening, exploration and analysis within VEsolve Pro, applying diverse machine learning algorithms. Finally, contingent on the selected algorithms, a wide spectrum of insights can be generated, encompassing layer thicknesses, electrical and mechanical surface properties, as well as the identification of defects and contaminants.
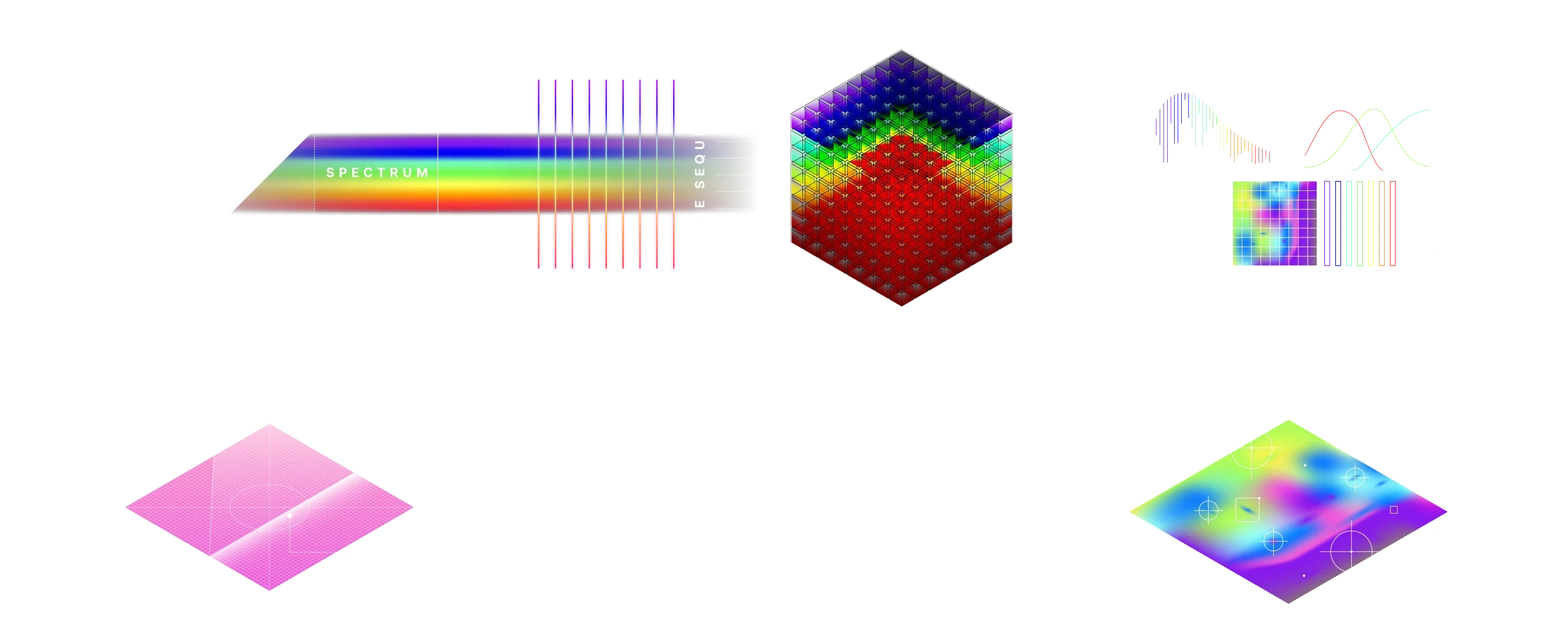
How the solution benefits our customers
Optimising production efficiency: In-line, hyperspectral imaging enables real-time layer thickness inspection facilitating immediate feedback and adjustments to process parameters
Thorough quality assessment: Hyperspectral imaging provides 100% surface coverage at a resolution of 170 µm
Enhanced Automation: In-line hyperspectral vision inspection eliminates the need for costly and time-consuming off-line inspection procedures
Product portfolio
VEpioneer and VEreveal systems provide spatially resolved property images of surfaces and thin films. Properties may include layer thickness, surface roughness, defects and contaminations, chemical, electrical and optical properties or any other type of quality criteria. The systems can be tailored to specific applications through customizable options for sample stage, excitation source, spectral ranges, cleanroom compatibility, and software interfaces.
Partnering with you
The DIVE imaging systems GmbH is a German manufacturer of innovative spectral imaging solutions. Our VEpioneer system is the world’s first fully integrated, one-button bench-top Hyperspectral Vision system, combining high-performance imaging with advanced data analysis to deliver insights within milliseconds. DIVE products deliver at-line and in-line inspection with highest precision and ultra-fast measuring speeds from nano- to micrometers.
We would like to thank our partners and funding bodies for their support. DIVE is funded by the Federal Ministry for Economic Affairs and Climate Protection and the European Social Fund as part of the EXIST research transfer program (funding reference: 03EUTSN217). DIVE is supported by the European Regional Development Fund and the Just Transition Fund.