Oct 1, 2024
Anti-Corrosion Layer Inspection for Metallic Bipolar Plates
Enhancing stability and performance of the physical vapor deposition process through measuring the anti-corrosion layer thickness in-line across the entire bipolar plate
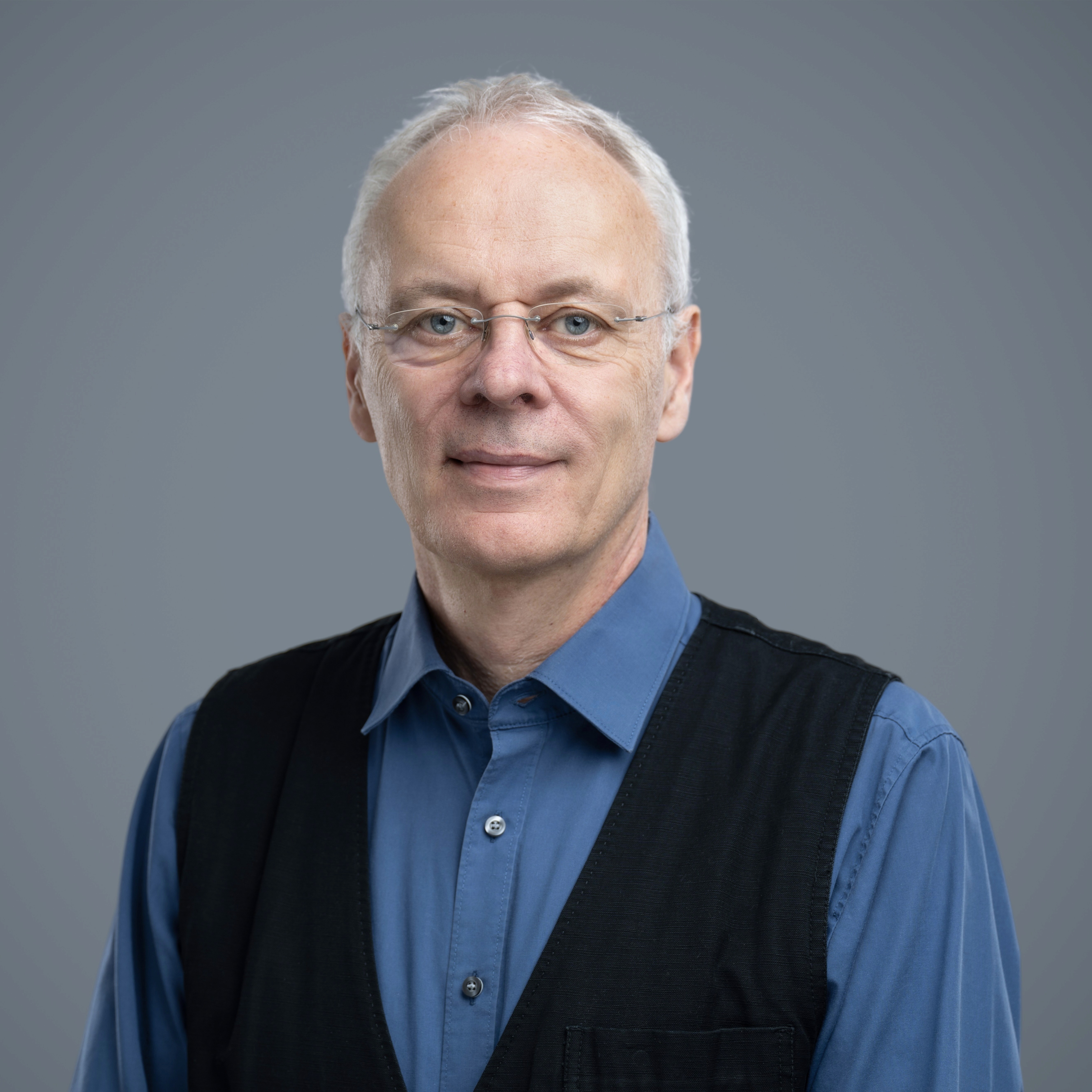
Dr. Wulf Grählert
Sales & Customer Care
Bipolar plates are key components in fuel cells and electrolysers, acting as separators between individual cells. Corrosion protection of metallic bipolar plates is crucial, as the surrounding water gradually degrades the material. Physical vapor deposition of carbon compounds such as Diamond-like carbon (DLC), Graphite-like carbon (GLC) or Tetrahedral Amorphous Carbon (Ta:C) provides protection, but layer thickness is critical. Insufficient layer thickness or defects lead to degradation and compromise longevity, while excessive thickness hinders performance.
The objective is to measure the thickness of an ultra-thin graphite-like carbon coating deposited on a structured stainless-steel substrate. Fabricated by Fraunhofer IWU and coated at Fraunhofer IWS DOC via physical vapor deposition, the GLC layer presents a thickness gradient of 0 to 50 nm along the 420 mm x 165 mm plate. Traditional metrology methods, including profilometry and ellipsometry, prove inadequate due to the coating's minimal thickness and the substrate's surface topography. Advanced laboratory techniques like glow discharge optical emission spectroscopy (GDOES) and focused ion beam scanning electron microscopy (FIB-SEM), while capable, are impractical for fast, comprehensive, and non-destructive inspection. FIB-SEM analysis of the bipolar plate's channel structure reveals a GLC layer thickness of approximately 30nm at one specific position (measurement by Nanores).
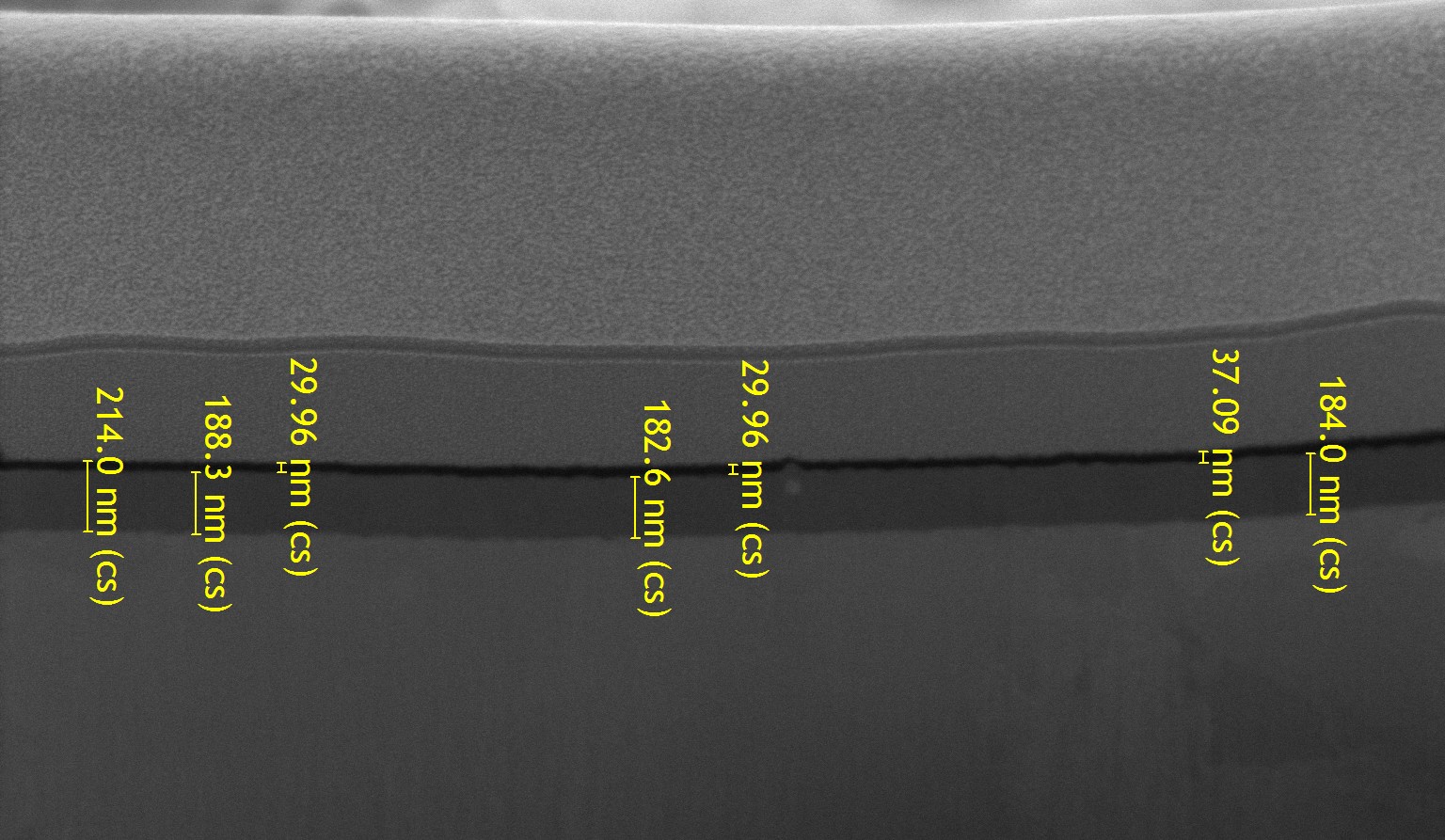
DIVE’s solution
Our at-line VEpioneer and in-line VEreveal systems allow to determine the GLC layer thickness on a structured bipolar plate with pixel-level precision (see image below). The entire bipolar plate is analysed in less than 20 seconds, with a spatial resolution of 300 µm per pixel. Results demonstrate a high degree of correlation with ground truth measurements obtained via FIB-SEM, exhibiting deviations of less than ±5% across the entire working range of 0 to 50 nm. The non-destructive nature of our Hyperspectral Vision technology enables both at-line and in-line quantification of anti-corrosion layer thickness.
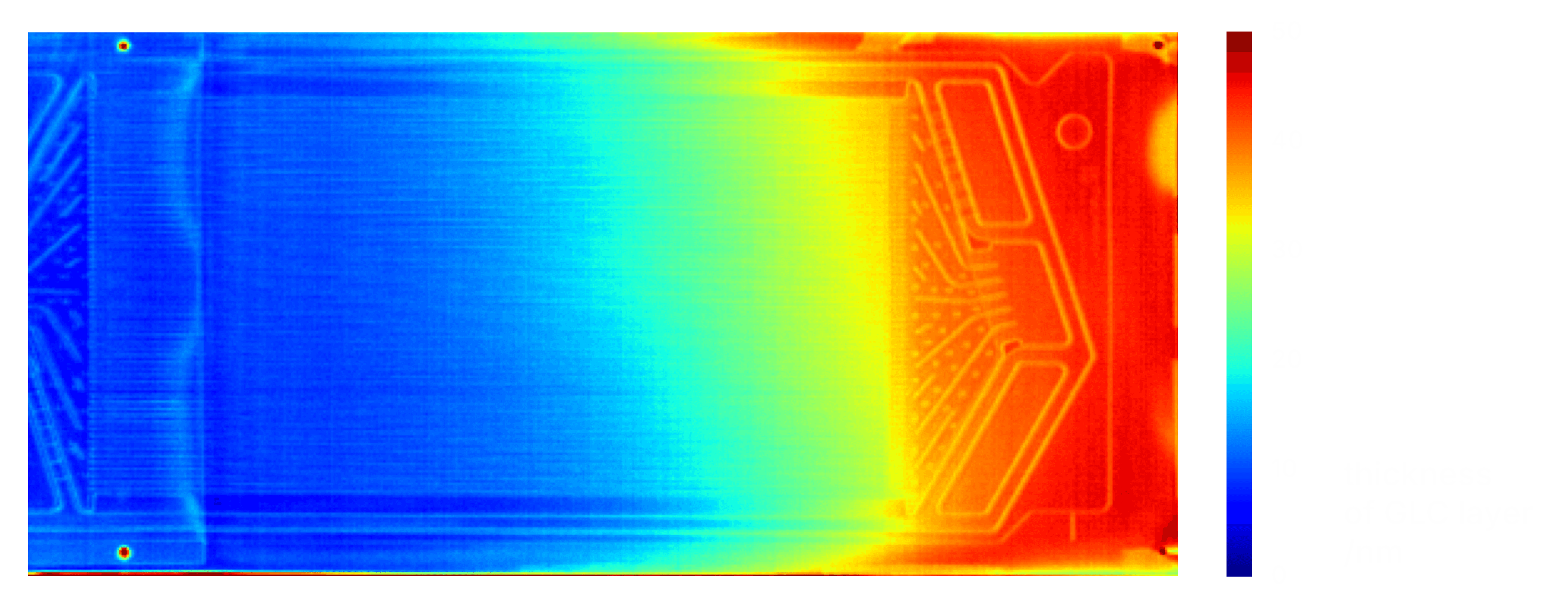
VEpioneer and VEreveal are built upon identical technological foundations and utilize our proprietary software suite, VEsolve Pro. The image below illustrates the operational workflow. Initially, data acquisition is performed via line-scan hyperspectral imaging, wherein the intensity of light reflected by the excited sample is measured. Spectral decomposition occurs within the camera, recording the intensity per pixel. Subsequent frame acquisition through sample translation results in the formation of the hyperspectral data cube. In the second phase, this data undergoes screening, exploration and analysis within VEsolve Pro, applying diverse machine learning algorithms. Finally, contingent on the selected algorithms, a wide spectrum of insights can be generated, encompassing layer thicknesses, electrical and mechanical surface properties, as well as the identification of defects and contaminants.
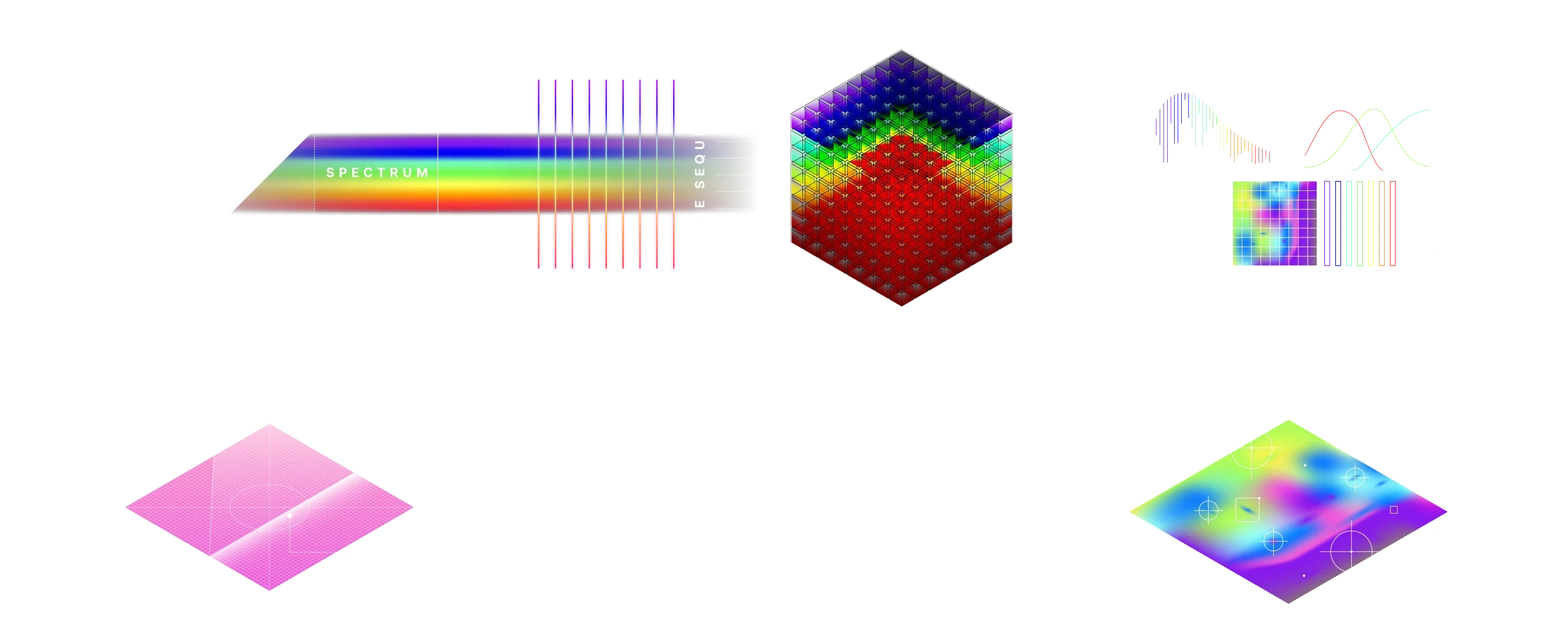
How the solution benefits our customers
Enhanced Fuel Cell Stack Performance: In-line inspection enables our customers to optimize the anti-corrosion layer thickness, resulting in improved fuel cell stack performance
Streamlined PVD Process Setup and Control: Fast and comprehensive access to layer thickness data across the entire bipolar plate accelerates PVD process setup, allows mitigating production fluctuations and variations, and improves overall reproducibility
Complete Traceability and Improved After-Sales Support: 100% inspection enables customers to track each bipolar plate throughout its lifecycle, facilitating improved after-sales support and failure analysis in the field
Product portfolio
VEpioneer and VEreveal systems provide spatially resolved property images of surfaces and thin films. Properties may include layer thickness, surface roughness, defects and contaminations, chemical, electrical and optical properties or any other type of quality criteria. The systems can be tailored to specific applications through customizable options for sample stage, excitation source, spectral ranges, cleanroom compatibility, and software interfaces.
Partnering with you
The DIVE imaging systems GmbH is a German manufacturer of innovative spectral imaging solutions. Our VEpioneer system is the world’s first fully integrated, one-button bench-top Hyperspectral Vision system, combining high-performance imaging with advanced data analysis to deliver insights within milliseconds. DIVE products deliver at-line and in-line inspection with highest precision and ultra-fast measuring speeds from nano- to micrometres.
We would like to thank our partners and funding bodies for their support. DIVE is funded by the Federal Ministry for Economic Affairs and Climate Protection and the European Social Fund as part of the EXIST research transfer program (funding reference: 03EUTSN217). DIVE is supported by the European Regional Development Fund and the Just Transition Fund.